
Ironmaking 101 From Ore to Iron with Blast Furnaces
Ironmaking Blast Furnace. Iron is made by reacting iron ore (iron oxide and impurities), coke (a reductant) and limestone (CaCO Blast furnaces are charged with iron ores in the form of pellets, sinter and/or lump ore and metallurgical coke in separate layers from the top of the furnace. Special Issue "Iron Ore Reactions and Phenomena in a Blast Furnace"
احصل على السعر
Blast Furnace Ironmaking an overview ScienceDirect
The blast furnace (BF) ironmaking process is currently the dominant process for providing steelmaking raw materials worldwide. However, the BF process This chapter discusses the blast furnace (BF), alternative and novel technologies for primary metal production. The chapter first gives information about iron, Recent developments in blast furnace iron-making technology
احصل على السعر
A Study on High-Grade Iron ore Beneficiation to Reduce
The study here highlights the optimization of beneficiation circuit for high-grade iron ore to attain higher productivity of both Pellet Plant and Blast Furnace with The reduction behavior of iron ores determines process efficiency, product quality and economy.The productivity and pollutant emission efficiency of blast furnace A Study on High-Grade Iron ore Beneficiation to Reduce Alumina
احصل على السعر
Blast furnace ironmaking and its ferrous burden quality
This chapter first gives an overview of the blast furnace ironmaking fundamentals including zones within the furnace and redox reactions involved, and In this paper, a novel methodology is proposed to implement the grain model to predict iron ore reduction in blast furnace. The model considers the gas Modeling of iron ore reactions in blast furnace
احصل على السعر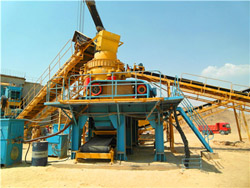
Technical Support Document for the Iron and Steel Sector:
iron and steel source category also includes taconite (iron ore) processing facilities, cokemaking facilities, and direct reduced ironmaking (DRI) facilities. There are eight taconite iron ore processing facilities that produced 52 million mt of pellets in 2007. 3, primarily for use in blast furnaces to make iron.Typical applications in iron ore processing as well as in sinter production are discussed with practical examples. Sintering is the most economic and widely used agglomeration process to prepare iron ore fines for blast furnace use. In this chapter, the sintering process is first described to identify the key steps of the process,Iron Ore ScienceDirect
احصل على السعر
Iron Ore Agglomeration Technologies IntechOpen
Until the 1950s of the last century, the oxidized iron ores that were loaded into the blast furnace had granulometries within 10 and 120 mm. However, the depletion of high-grade iron ore sources has The current state of briquetting technology in iron smelting processes is assessed. For the first time, the importance of using ore-coal briquettes for the charge in blast furnace processes as a means of reducing the total carbon consumption and emissions of CO2 is shown. The role of solid-state reduction in blast-furnace ore-coal Use of Ore-Coal Briquettes in Blast Furnaces SpringerLink
احصل على السعر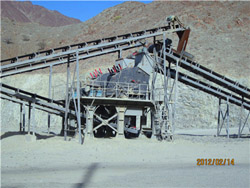
Blast Furnace OSRS Wiki
On Blast Furnace themed worlds, there is an additional 72,000 coins fee to use the Blast Furnace for one hour; the fee is deposited in the coffer near the bank chest. On all other worlds, there is no extra fee but players must work together to operate the Blast Furnace. While bars will cool down on their own with time, a bucket of water can be used at the More than ninety per cent of Australia’s current iron ore exports are mined from the deep red weathered Pilbara landscape in Western Australia and over 70 per cent of this material is shipped to China, where it is made into iron in blast furnaces using coke manufactured from coal, then further processed into steel.. Australia mines almost half Steeling ourselves: How Australia can support the transition to net
احصل على السعر
Extraction of Iron Metallurgy Blast Furnace and Reactions
It’s a long process which begins with Concentration through calcination roasting. Concentration removes the water and other volatile impurities such as sulphur and carbonates. This concentrated ore is mixed with limestone (CaCO 3) and Coke and fed into the blast furnace from the top. It is in the blast furnace that extraction of iron occurs.Iron ore pellets are small and hard spherical particles agglomerated from a fine iron ore concentrate. They are used in the blast furnace process to produce hot metal. The diameter of blast furnace pellets is usually between 8 and 16 mm. In this study, a batch of magnesia iron ore pellets was first sieved into particle sizes of 8–10 mm, 10–12.7 Effect of Iron Ore Pellet Size on Metallurgical Properties MDPI
احصل على السعر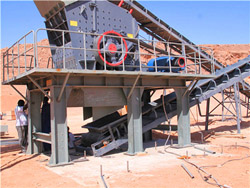
Recent Trends in the Technologies of the Direct Reduction and
The blast furnace and direct reduction processes have been the major iron production routes for various iron ores (i.e. goethite, hematite, magnetite, maghemite, siderite, etc.) in the past few decades, but the challenges of maintaining the iron and steel-making processes are enormous. The challenges, such as cumbersome production Iron processing Smelting, Refining, Alloying: The primary objective of iron making is to release iron from chemical combination with oxygen, and, since the blast furnace is much the most efficient process, it receives the most attention here. Alternative methods known as direct reduction are used in over a score of countries, but less than 5 percent of iron is Iron processing Smelting, Refining, Alloying Britannica
احصل على السعر
Iron ore sintering ScienceDirect
Sintering is the most economic and widely used agglomeration process to prepare iron ore fines for blast furnace use. In this chapter, the sintering process is first described to identify the key steps of the process, that is, granulation and thermal densification. Discussion is then focused on the effect of the chemical, physical, andTraditional integrated steel making processes use ore containing iron oxide (“iron ore”) as feed materials for blast furnaces. The ore is fed into blast furnaces together with a reductant material such as coke and is converted in the blast furnaces into molten iron that is then used in other steel making processes, such as in basic oxygen furnaces to US20070157761A1 Use of an induction furnace for the production
احصل على السعر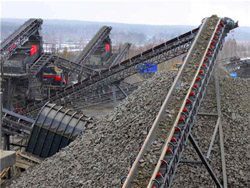
A Study on High-Grade Iron ore Beneficiation to Reduce Alumina
A typical high-alumina containing iron ore slime from the eastern Indian sector containing 58.13% Fe, 6.48% SiO2, 4.9 % Al2O3 and 5.35% LOI, have been evaluated to find out whether grinding of thePublished Jul 17, 2023. + Follow. Iron ore extraction typically occurs in a blast furnace using coke as a fuel and limestone as a flux. First, the ore is heated with a reducing agent, such as cokeHow is iron extracted from ore in an industrial process? LinkedIn
احصل على السعر
PROSPECTIVE OF TITANIA- MAGNETITE ORE PROCESSING IN BLAST FURNACE
Key words: Titania-magnetite ore; Blast furnace; Rotary hearth; ITmk3 process. 1 Technical contribution to the 6th International Congress on the Science and Technology of Ironmaking ICSTI, 42nd International Meeting on Ironmaking and 13th International Symposium on Iron Ore, October 14th to 18th, 2012, Rio de Janeiro, RJ, Brazil. 2 Hatch.Iron ore pellets are largely characterized by inherent physical and chemical properties of the ore. Alumina and silica play important roles in determining the productivity of a Blast Furnace. On average, one percent increase in iron content improves productivity by 2% and reduces coke consumption by 1%. Therefore higher iron ore feed A Study on High-Grade Iron ore Beneficiation to Reduce
احصل على السعر
Recent developments in blast furnace iron-making technology
This chapter discusses the blast furnace (BF) iron making. The chapter first gives information about fundamentals and historical development of BF technology and design and its role in the steel industry. It then discusses the chemical and physical processes in the BF with focus on the reduction of burden materials, processes in the J.X. Feng et al., Drying and preheating processes of iron ore pellets in a traveling grate 537. 3.2. Governing equations. (1) Gas energy conservation equation. To deduce the heat exchange equation(PDF) Drying and preheating processes of iron ore pellets in a
احصل على السعر
Use of HBI in Blast Furnace SpringerLink
HBI is a pre-reduced material and therefore less iron oxide to be reduced is in the blast furnace. Because the percentage of CO and H 2 in the gas is higher with the use of HBI, the calorific value increases slightly up to 1.5%. Fig. 6. Development of gas utilization with HBI. Full size image.Resource Recovery and Recycling from Metallurgical Wastes. S. Ramachandra Rao, in Waste Management Series, 2006 9.8 Production of Ceramic Tiles from Iron Ore Tailings. Current practice of washing iron ore before it is processed for extractive metallurgical operation results in three products, coarse ore lumps with sizes in the range 10-80 mm, Iron Ore Processing an overview ScienceDirect Topics
احصل على السعر