
Tube mill Polysius
Tube mill Tube mills are used for wet grinding iron ore, gold/copper ore, nickel ore and other ores, as well as for grinding lime/limestone for flue gas desulphurisation systems, The centrifugal tube mill is a single-tube mill with a grinding tube length of 2200 mm and a diameter of 350 mm, which describes a defined oscillatory Centrifugal tube mill for finest grinding ScienceDirect
احصل على السعر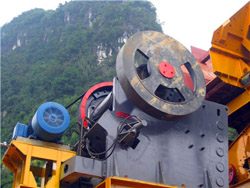
Centrifugal tube mill for finest grinding ScienceDirect
The similar pitches of the regression line show that the grinding behaviour of limestone under the specific action principles of the centrifugal tube mill Williams Crusher’s limestone mills and Pulverizers offer solutions for various size-reduction applications. We design & manufacture the most durable & efficient limestone crushing machines on the market. Contact Limestone Mills Limestone Crushers & Pulverizers
احصل على السعر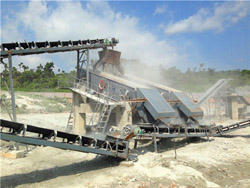
Limestone mill, Limestone grinding mill All industrial
Find your limestone mill easily amongst the 60 products from the leading brands (TON, TON, NEUE HERBOLD,) on DirectIndustry, the industry specialist for your Limestone is burnt to calcium oxide (quicklime) and in a second step water is added to create hydrated lime. Bauermeister mills can be used for grinding natural limestone as well as burnt lime to the desired particle Limestone Minerals Applications Hamburg
احصل على السعر
A study of the grinding of magnetite/limestone mixture in
In this paper, batch studies were carried out by grinding magnetite, limestone, and magnetite/limestone mixture at different mixing ratios in a laboratory PDF Fine and ultrafine grinding of limestone are frequently used in the pharmaceutical, chemical, construction, food, and cosmetic industries, Find, read and Energy-Model and Life Cycle-Model for Grinding Processes of
احصل على السعر
The effect of grinding aids on the fine grinding of limestone,
The main focus of this study was to investigate both aspects within one single study: On the one hand, dry fine grinding of limestone was investigated in a dry between grinding fineness and specific grinding work for limestone, andesite, pumice, and tailings of ore processing in a laboratory stirred ball mill. Figure 2.Energy-Model and Life Cycle-Model for Grinding Processes of Limestone
احصل على السعر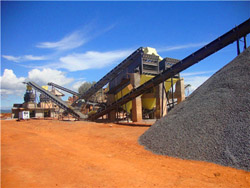
11.6 Portland Cement Manufacturing U.S. Environmental
H. Raw material grinding/drying -13 I. Clinker cooler -14 J. Clinker piles -15 K. Clinker transfer -16 L. Clinker grinding -17 M. Cement silos -18 N. Cement load out -19 O. Raw mill feed belt -24 P. Raw mill weigh hopper -25 Q. Raw mill air seperator -26 R. Finish grinding mill feed belt -27 S. Finish grinding mill weight hopper -283/22 Mineral Products Industry 11.6-5 In the wet process, water is added to the raw mill during the grinding of the raw materials in ball or tube mills, thereby producing a pumpable slurry, or slip, of approximately 65 percent solids.11.6 Portland Cement Manufacturing U.S. Environmental
احصل على السعر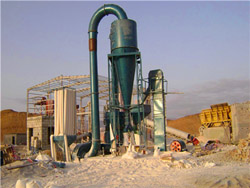
Resistance to Grinding and Cement Paste Performance of Blends
Even though not practical mixtures such as C 100 G 0 were evaluated in this work, this was purely from a mathematical point of view in order to obtain a better sampling of the independent variables (i.e. the mixture composition) using a simplex-centroid design.. Resistance to Grinding. A total of 700 ml of each blend were introduced in a Approximately 84.00% clinker, 4.00% gypsum, and 7.00% limestone are sent into a roller crusher to achieve a preliminary size reduction in the final stage. Next, these materials from the roller crusher with fly ash Analysis of material flow and consumption in cement
احصل على السعر
Energy-Efficient Technologies in Cement Grinding IntechOpen
The energy consumption of the total grinding plant can be reduced by 20–30 % for cement clinker and 30–40 % for other raw materials. The overall grinding circuit efficiency and stability are improved. The maintenance cost of the ball mill is reduced as the lifetime of grinding media and partition grates is extended. 2.5.The limestone and clay are ground separately to a size of about 25 mm in crushers. Then it is pulverized into fine powder in ball mills and tube mills. The crushing and pulverizing process is carried out separately for each material. After grinding, each of the materials is stored in hoppers. 2. Mixing & Storage2 Process of Manufacture of Cement Civil Giant
احصل على السعر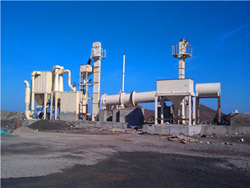
Energy-Efficient Advanced Ultrafine Grinding of Particles Using
The present literature review explores the energy-efficient ultrafine grinding of particles using stirred mills. The review provides an overview of the different techniques for size reduction and the impact of energy requirements on the choice of stirred mills. It also discusses the factors, including the design, operating parameters, and feed Table 2 shows, as an example, the advantages of the eccentric vibratory mill in comparison to a conventional tubular vibratory mill for ultrafine grinding of limestone. With the eccentric vibratory mill 656-2ks, the throughput can be raised by a factor of 2 at half the grinding chamber volume of the double-tube vibratory mill.Eccentric vibratory mills — theory and practice ScienceDirect
احصل على السعر
Grinding With Tube Mill PDF Building Engineering Cement
234626714-Grinding-With-Tube-Mill.ppt Free download as Powerpoint Presentation (.ppt), PDF File (.pdf), Text File (.txt) Grinding Technology of Limestone With Ball Mills. Grinding Technology of Limestone With Ball Mills. anrulo. Laporan Analysis Report. Laporan Analysis Report. aprilia. Donner Company.H. Raw material grinding/drying -13 I. Clinker cooler -14 J. Clinker piles -15 K. Clinker transfer -16 L. Clinker grinding -17 M. Cement silos -18 N. Cement load out -19 O. Raw mill feed belt -24 P. Raw mill weigh hopper -25 Q. Raw mill air seperator -26 R. Finish grinding mill feed belt -27 S. Finish grinding mill weight hopper -2811.6 Portland Cement Manufacturing U.S. Environmental
احصل على السعر
A study of the grinding of magnetite/limestone mixture in a
In this paper, batch studies were carried out by grinding magnetite, limestone, and magnetite/limestone mixture at different mixing ratios in a laboratory-scale stirred mill. The impact of mixing ratios on the volume fraction of the desired size (−45 + 10 μm) in the ground products, energy consumption, and residence time of the feed in the limestone processing grinding machine is the best machine for limestone powder make.can reached 300-3000 mesh .if you are interesting in this machine ,please...limestone processing machine-limestone grinding mill machine
احصل على السعر
How to choose between ball mill and vertical roller mill?
4. Grinding process. In the ball mill, the material is mainly crushed by impact and friction. In the vertical grinding mill, the material is mainly extrusion, and grinding is the auxiliary. The residence time of the material in the vertical mill is 2-3 minutes, while in the ball mill it takes 15-20 minutes.Experience has shown that the best grinding conditions for ores in ball mills are created by a slurry density of between 70% and 80% solids by mass [15,16]. This implies that the milling rates are highest within this range. We investigated the effects of slurry density, grinding time and grinding energy on the grindability of a typical platinumSlurry density effects on ball milling in a laboratory ball mill
احصل على السعر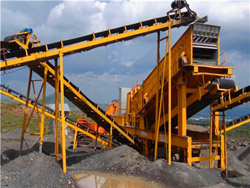
Ball Mills 911 Metallurgist
Tube Mills. Tube mills are in principle to be considered as ball mills, the basic difference being that the length/diameter ratio is greater (3—5). They are commonly used for surface cleaning or scrubbing action and fine grinding in open circuit. Pebble Mills. In some cases it is suitable to use screened fractions of the material as grindingUS2991017A Grinding method in ball, tube and other mills Google Patents Grinding method in ball, tube and other mills Download PDF Info Publication number US2991017A Experiment 1 Crushed limestone was ground at Grinding method in ball, tube and other mills Google Patents
احصل على السعر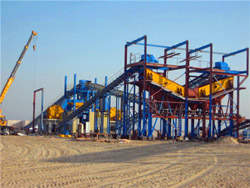
Vertical mill process limestone powder preparation techniques
As a FGD process with limestone desulfurization agent, lime stone powder through dissolving solid — liquid two-phase reaction, the reaction rate and limestone particle specific surface area isFor example, instead of regrinding the separator reject in the tube mill, it can be directed to a stirred mill. Thus a possible energy saving can be obtained compared to ball mill grinding. Because, stirred mills are reported to supply energy savings below 100 μm product sizes [5] such as for finish cement (−30 μm).Open and closed circuit dry grinding of cement mill rejects in a
احصل على السعر