
Operational parameters affecting the vertical roller mill
Grinding test results for zinc ore showed that it is possible to decrease the total grinding energy consumption from 20.11 to 11.40 kW h/t by using vertical roller mill instead of AG/SAG-ball mill circuit ( van Drunick et al., 2010 ).The simulations reveal that compared to normal MPC, soft MPC regulate cement mill circuits better and in a plant friendly way (PDF) Cement mill optimization: Design parameters
احصل على السعر
Review on vertical roller mill in cement industry & its
All grinding processes in the cement industry are operated dry. The capacities of grinding mills range from 300 − 1000 TPH for Limestone and for cement The cement industry uses a wide range of different systems in raw material, coal, and cement grinding. While new plants mainly focus on highly energy‑efficient systems, Thomas Holzinger, Holzinger Consulting, grinding system
احصل على السعر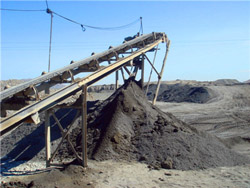
OPTIMIZATION OF CEMENT GRINDING OPERATION IN BALL MILLS
Cement ball mills typically have two grinding chambers. The first chamber is filled with larger diameter grinding media and lined with lifting liners. The first chamber coarse The modular vertical roller mill for grinding cement raw material, cement clinker, and additives with an installed power of up to 12,000 kW was specifically Grinding process optimization IEEE Xplore
احصل على السعر
Energy and exergy analyses for a cement ball mill of a
This research focuses on investigating the effects of the three different grinding aids, consisting of a mixture of amine, glycol and polyol in different ratios, Cement production is one of the most energy‑intensive manufacturing industries, and the milling circuit of cement plants consumes around 4% of a year’s global electrical energy Modeling of energy consumption factors for an industrial cement
احصل على السعر
Effects of grinding aids on model parameters of a cement
In this context, three different types of grinding aids were tested at various dosages in a cement plant and the impacts of grinding aids on model parameters of This research focuses on investigating the effects of the three different grinding aids, consisting of a mixture of amine, glycol and polyol in different ratios, on the model parameters of a two-compartment cement ball mill and an air classifier. Within the content of this work, sampling campaigns were organized around a cement grinding Effects of grinding aids on model parameters of a cement ball mill
احصل على السعر
Efficiency of Using Small Diameter Grinding Balls for Cement Grinding
Abstract The results of industrial tests of ShKh15steel grinding balls with diameters of 25, 30, and 35 mm of 5th hardness group as per GOST (State Standard) 7524–2015 at AO Kharkiv Pilot Cement Plant during grinding of cement in the second chamber of a cement mill are presented. It is shown that the use of ShKh15 steel The proposed solution has been deployed in a number of cement plants around data-driven approach utilizing real-time monitoring control technology is proposed for the purpose of optimizing the grinding of cement For example, the time lag between mill parameters (i.e., FRF, MIF, MOF, and BEA), and coarse return variedCoarse Return Prediction in a Cement Industry’s Closed Grinding
احصل على السعر
Energy-Efficient Technologies in Cement Grinding IntechOpen
The energy consumption of the total grinding plant can be reduced by 20–30 % for cement clinker and 30–40 % for other raw materials. The overall grinding circuit efficiency and stability are improved. The maintenance cost of the ball mill is reduced as the lifetime of grinding media and partition grates is extended. 2.5.Milling operations in various production processes are among the most important factors in determining the quality, stability, and consumption of energy. Optimizing and stabilizing the milling process is a non-linear multivariable control problem. In specific processes that deal with natural materials (e.g., cement, pulp and paper, beverage Coarse Return Prediction in a Cement Industry’s Closed Grinding
احصل على السعر
Coal Grinding Cement Plant Optimization
Coal Grinding. To achieve good combustion and satisfactory flame formation, coal needs to be dried and ground to a proper degree of dryness and fineness. Drying of moisture in coal is achieved normally by ducting part of the kiln exhaust gas through the mill with inlet temperatures of up to 300°C. Inert kiln exhaust gases with oxygen contentNowadays, ball mills are used widely in cement plants to grind clinker and gypsum to produce cement. In this work, the energy and exergy analyses of a cement ball mill (CBM) were performed andEnergy and exergy analyses for a cement ball mill of a
احصل على السعر
(PDF) Determination of correlation between specific energy consumption
Some investigations observed that VRM installation in grinding saves 30% of cement mill energy with ease of control and reduces the mill start-up/shut down durations [1,2,3, 4, 5].Intelligent Modeling of Cement Plant Mill Unit Using Artificial Neural Networks and Real Data. 10.1109/SIBCON50419.2021.9438907. Conference: 2021 International Siberian Conference on Control and(PDF) Intelligent Modeling of Cement Plant Mill Unit Using
احصل على السعر
Cement Grinding Cement Plant Optimization
Water Spray in Cement Mills. Water spray installed generally in second compartment of ball mill to control cement temperature. Cement discharge temperature should be kept below about 110 o C but, the same time should allow some 60% dehydration of gypsum to optimize cement strength without excessive false set.Cement Plant Operations Handbook 15. only) for soft, chalky limestone to 25kWh/t for hard materials. System power consumption is typically 30% lower in roller mills, and combined power consumption may be 10-30% lower if a roll press or Cement Plant Operation Handbook PDF Mill (Grinding) Scribd
احصل على السعر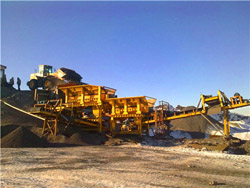
Quantifying the effect of clinker grinding aids under laboratory
The effect of clinker grinding aids (GAs) on mill performance and cement properties is currently quantified in real-scale grinding plants. In fact, laboratory-grinding mills operated for given time interval do not consider the effect of circulating load, thereby leading to increased specific energy consumption (Ec) with excessively wide cement Now a days Cement plants are producing 75–80% PPC & 20–25% OPC due to high market demand of PPC. Production of PPC is cheaper and it's market rate is also lower than OPC by nearly 25 rupees per bag, so general consumer are attracted towards PPC cement. Cement companies also want to produce more and more PPC Review on vertical roller mill in cement industry & its performance
احصل على السعر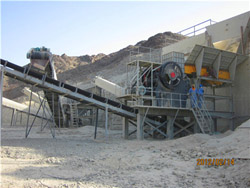
Effects of Mill Speed and Air Classifier Speed on Performance of
Optimum performance of ball mill could potentially refine Blaine fineness, thereby improving the cement quality. This study investigates the effects of separator speed and mill speed on BlaineKeywords: Vertical roller mill, cement grinding, performance evaluation INTRODUCTION Cement production is highly energy consuming process with energy utilization of around 110-150 kWh/t (Villa, 2005).Performance Evaluation of Vertical Roller Mill in Cement Grinding
احصل على السعر
Digitization and the future of the cement plant McKinsey
According to our analyses, the cement plant of the future could reduce emissions by up to 75 percent by 2050 compared with 2017. Around 20 percent will come from operational advances, such as energy-efficiency measures and clinker substitution. An additional 10 percent will come from alternative fuels—however, the availability of Finished grinding may consume 25-50 kWh/t cement, depending on the feed material grindability, additives used, plant design and especially the required cement fineness. The grinding process absorbs more energy due to the losses attributable to heat generated during grinding, friction wear, sound noise and vibration.Blended Cement Grinding: Energy Intake and Fineness
احصل على السعر
Full article: Evaluation of optimization techniques for predicting
1. Introduction. Cement manufacturers face economic and environmental challenges due to their high-energy consumption. Periodic data collection on industry and other energy-consuming industries is crucial to setting objectives for energy-saving studies (Madlool, Saidur et al., Citation 2013).Atmaca and Yumrutaş (Citation 2014) suggested that an It has been established that about 7–10% of the cement can be lost due to uncontrolled emissions in the cement mill [ 21 ]. Some studies show that 4–5% of dust emissions are due to the furnace’s supply, while other dust emission sources are crushers, clinker coolers, grinding, and material handling equipment [ 35 ].Dust Emission Monitoring in Cement Plant Mills: A Case Study
احصل على السعر
Technological Energy Efficiency Improvements in Cement Industries
The cement industry is highly energy-intensive, consuming approximately 7% of global industrial energy consumption each year. Improving production technology is a good strategy to reduce the energy needs of a cement plant. The market offers a wide variety of alternative solutions; besides, the literature already provides reviews of
احصل على السعر