
Design of a crushing system that improves the crushing
There are three main steps in designing a good crushing plant: process design, equipment selection, and layout. The paper analyses all of these steps Keywords To study and optimize the gyratory crusher performance, taking the process of crushing iron ore by the gyratory crusher as the specific analysis object in this Simulation and optimization of gyratory crusher
احصل على السعر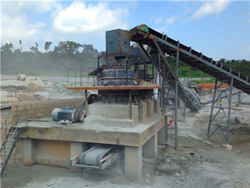
(PDF) DESIGN AND OPERATIONS CHALLENGES OF
PDF A review on the design and operations challenges of a single toggle jaw crusher is presented. Strength and fracture toughness of the material to Find, read and cite all the research youUniaxial compressive strength (UCS) is a key physical test relevant to iron ore crusher design and rock geomechanics for mining. Tests are typically performed on intact lengths Uniaxial Compressive Strength an overview ScienceDirect
احصل على السعر
Chamber Optimization for Comprehensive
Published 15 Mar 2021 Abstract This study aims to analyze the impact of key structural parameters such as the bottom angle of the mantle, the length of the parallel zone, and the eccentric angle on the productivity and Crusher Guoguang Li, Boqiang Shi, Ruiyue Liu et al.-An Experimental Research of Biomass Crushing System Yue Xia-Optimization Design and Simulation Crusher &RQH&UXVKHU IOPscience
احصل على السعر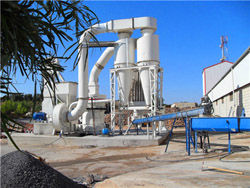
Optimisation of the swinging jaw design for a single toggle jaw crusher
Abstract. This study reports on the design optimisation of the swinging jaw crusher plate. Jaw crusher machines are used in the mining and construction industry for The following step could be its application in the design of a customized jaw crusher with the aim of improving crusher performance. This could represent, for instance, setting the crusher frequency and DEM Simulation of Laboratory-Scale Jaw Crushing
احصل على السعر
Crusher an overview ScienceDirect Topics
13.3.1.1 Primary Crusher. Primary crushers are heavy-duty rugged machines used to crush ROM ore of (−) 1.5 m size. These large-sized ores are reduced at the primary crushing Comminution by gyratory crusher is the first stage in the size reduction operation in mineral processing. In the copper industry, these machines are widely utilized, and their reliability has become a relevant aspect. To optimize the design and to improve the availability of gyratory crushers, it is necessary to calculate their power and torque Minerals Free Full-Text Torque Analysis of a Gyratory Crusher
احصل على السعر
Optimisation of the swinging jaw design for a single toggle jaw crusher
The plate dimensions of the un-optimised jaw crusher were modelled using ANSYS Design Modeller 2021, as shown in Fig. 3.The load and boundary conditions for the static structural analysis were as shown in Fig. 4.Design of Experiments (DoE) was then conducted where the minimum and maximum values of the target parameters were The design parameters of the crusher include the size of the top opening, the set, the volume of the crushing chamber, and the type of jaw surface, which may be smooth or corrugated . The equipment DEM Simulation of Laboratory-Scale Jaw Crushing
احصل على السعر
Crushing Plant Flowsheet & Design-Layout 911 Metallurgist
Crushing Plant Flowsheet & Design-Layout. In the crushing section, the ore as it comes from the mine is broken down dry to a size suitable for the wet grinding machines ; these can, if necessary, be made to take lumps of 2-in. size, but they work much more efficiently if their feed is ½ in. or less. Before the advent of the Symons cone Ore blending is an essential part of daily work in the concentrator. Qualified ore dressing products can make the ore dressing more smoothly. The existing ore blending modeling usually only considers the quality of ore blending products and ignores the effect of ore blending on ore dressing. This research proposes an ore blending modeling method Applied Sciences Free Full-Text A Method of Ore Blending
احصل على السعر
(PDF) The Influence of the Structure of Double Toothed Roller Crusher
The best test scheme and the order of three influencing factors are obtained, which provides the basis for the design of the double toothed roller crusher. Uniaxial compression model Figure 4.Roll Crushers. In Mineral Processing Design and Operations (Second Edition), 2016. 6.2.3 Roll crusher circuit design. Roll crushers are generally not used as primary crushers for hard ores. Even for softer ores, such as chalcocite and chalcopyrite, they have been used as secondary crushers. Choke feeding is not advisable as it tends to produce particles of Roll Crusher an overview ScienceDirect Topics
احصل على السعر
Self-tuning control of an ore crusher ScienceDirect
An industrial application is described where a self-tuning regulator is used for control of an ore crusher. There are difficult control problems associated with this process due to significant variations in operating conditions and long time delays in the system. The design of a self-tuning regulator for the crusher is discussed in detail.The paper shows the preparation of the numerical models necessary for the simulation mapping of industrial-scale crushers of problematic material, such as copper ore with complex lithology. The crushers investigated in this work are located in the KGHM Polska Miedz S.A. copper ore processing plant. The complex ore consisting of Minerals Free Full-Text Industry Scale Optimization: Hammer Crusher
احصل على السعر
What equipment is used in iron ore crusher? LinkedIn
Here are some common types of equipment used in iron ore crushing: 1. Jaw Crusher: This is a primary crusher that is used for coarse crushing. It has a fixed jaw plate and a movable jaw plate, andThe first step of physical beneficiation is crushing and grinding the iron ore to its liberation size, the maximum size where individual particles of gangue are separated from the iron minerals. A flow sheet of a typical iron ore crushing and grinding circuit is shown in Figure 1.2.2 (based on Ref. [4]).This type of flow sheet is usually followed when the crude ore Crushing Circuit an overview ScienceDirect Topics
احصل على السعر
Crushing TON
The crushers are built to perform with the lowest cost per ton, featuring a unique combination of crusher cavity design, crushing forces, reliability and safety. Engineered spare and wear parts as well as maintenance and optimization services are designed with decades of experience in different crushers and crushing processes.The ore entering the crusher will affect . the plant performance, based on its change in . This paper addresses the critical design parameters as well as the consideration of ore(PDF) Factors affecting the performance of
احصل على السعر
(PDF) Design and Construction of Rock Crushing Machine
Chermileusky EV, Romanor VA (1994) Cone crusher performance Ph D thesis department of machine and vehicle design, Chalmers University Of Technology, Sweden. Mechanical engineers hand book 1570-1572The crushing of minerals and ore is of great industrial importance. With global population growth, urbanization, and continuing improvements in living conditions, the productivity and efficiency of existing crushers must be increased to meet the growing demand [].Cone crushers are characterized by a continuous operating cycle and may Forces in a Cone Crusher SpringerLink
احصل على السعر
Industrial Solutions Jaw crushers ThyssenKrupp
• Ore mining industry • Ore crushing in metallurgical plants • Recycling industry • Other areas of the primary industry Design characteristics • Crusher frame and swing jaw made of high-grade steel or special cast steel that has been subjected to a stress- relieving heat treatment in order to pre vent residual stresses from the welding13.3.1.1 Primary Crusher. Primary crushers are heavy-duty rugged machines used to crush ROM ore of (−) 1.5 m size. These large-sized ores are reduced at the primary crushing stage for an output product dimension of 10–20 cm. The Crusher an overview ScienceDirect Topics
احصل على السعر
Jaw Crusher ScienceDirect
The ore or rock is fed to the crusher where the jaws are furtherest apart, i.e., at the maximum opening or gape. The rule of thumb applicable for operating a jaw crusher with respect to its design characteristics can be summarised as follows: Feed size = 0.8–0.9 × gape: Reduction ratio, R = 1:4 to 1:7: Throw, L TThe design and construction of a prototype rock crushing machine was performed this is with a view to ensuring that the designed crusher is capable of crushing rocks, lime stone and solid minerals for indigenous use. The research work was tailored mainly on the design and production of locally fabricated rock crushing machine for Design and Construction of Rock Crushing Machine from
احصل على السعر
Crusher &RQH&UXVKHU IOPscience
Crusher Guoguang Li, Boqiang Shi, Ruiyue Liu et al.-An Experimental Research of Biomass Crushing System Yue Xia-Optimization Design and Simulation Analysis for Cavity Shape of Single Toggle Jaw Crusher Xiaoqin Zhong, Xiaojian Niu, Qiqiang Ji et Crushing is the process of reducing the size of ore into definite smaller
احصل على السعر