
Modernizing cement manufacturing in China leads to
The cement manufacturing process mainly includes four steps: resource extraction, raw material preparation, clinker calcination, cement grinding 17,18, and fossil 1. As a fuel in the production of cement clinker, 2. Ash produced by burning coal in power stations is used as a component in cement rotary kiln feeds, 3. Ash Coal utilisation in the cement and concrete industries
احصل على السعر
Cement Mill Cement Grinding Machine AGICO
Coal mill is the main equipment in the pulverized coal preparation process.Because calcining top-grade cement clinker requires a stable supply of coal powder as the fuel of cement kiln, and more than 85% of Fig. 3 shows that grinding (finish and raw grinding) consumes major share (i.e. 60%) of total energy consumption in a cement manufacturing process. This can be A critical review on energy use and savings in the cement industries
احصل على السعر
Cement mill, Cement grinding mill All industrial
Motor power: 403 kW. Sound pressure: 77, 96, 117 dB. The TG5000 tub grinder from Vermeer is your machine for powerful processing in a convenient package, with a 540 hp Life-cycle assessment framework for cement manufacturing The value chain of cement manufacturing includes four steps: resource extraction, raw material preparation, clinker burning, and (PDF) Modernizing cement manufacturing in
احصل على السعر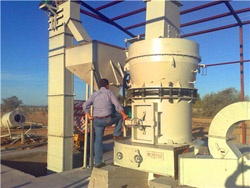
Recent development on the uses of alternative fuels in cement
The cement manufacturing industry is under increasing pressure from the environmental protection agencies to reduce the emissions. The usage of alternative The type of fuel used in cement manufacture directly impacts on CO 2 emissions, with coal accounting for around 60–70% of CO 2 emissions from cement CO2 Capture Technologies for Cement Industry ScienceDirect
احصل على السعر
Cement Production Technologies Thermo Fisher Scientific IN
Satisfy customer specifications for high quality coal blends while achieving more cost-effective, efficient operations.The Thermo Scientific COBOS Coal Blend Optimization cement production or (partial) substitution of cement in concrete production reduces these CO2 emissions, especially if material is used which is seen as a waste of other processes, such as Fly Ash (FA) from coal power plants and Granulated Blast Furnace Slag (GBFS) from the iron and steel sector. These materials are currently used Fly ash and Blast Furnace Slag for Cement
احصل على السعر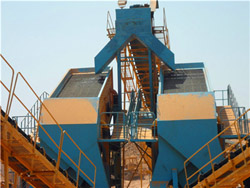
Cement Analysis and Production Information Thermo
The cement production process begins with the extraction of limestone and clay from the quarry. The material is then blended, crushed and fed to the kiln. Post-kiln, the clinker is cooled and goes through a final grinding method before it is ready to ship. Portland cement, the most common type of cement, is formulated in a variety of strengthsRefuse-derived fuel (RDF) from municipal solid waste (MSW) is an alternative fuel (AF) partially replacing coal/petcoke in a calciner/kiln of cement plant. The maximum thermal substitution rate (TSR) achieved through RDF is 80–100% in the calciner, while it is limited to 50–60% in the kiln burner. Different AF pre-combustion technologies, Recent Progress in Refuse Derived Fuel (RDF) Co-processing in Cement
احصل على السعر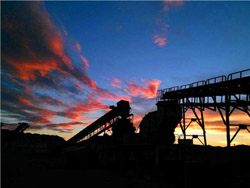
Coal utilisation in the cement and concrete industries
Cement manufacturing process15.3.1. Make-up of Portland cement. Portland cement is a fine powder produced by grinding Portland cement clinker (more than 90%), a limited amount of gypsum (calcium sulphate dehydrate CaSO4.2H2O, which controls the set time) and other minor constituents which can be used to vary the Grinding is a highly energy intensive process in the cement industry. Approximately 60–70% of the total electrical energy used in a cement plant is utilized for the grinding of raw materials, coal and clinker [63]. The electrical energy consumed in cement production is approximately 110 kWh/tonne.A critical review on energy use and savings in the cement industries
احصل على السعر
POWERING THE CEMENT INDUSTRY CEMBUREAU
CEMENT SECTOR POWERING THE CEMENT INDUSTRY . Cement is an energy-intensive industry, but currently, electricity accounts for circa 12% within the energy mix, while the rest is various fuels. Total electricity consumption in a dry process is split into equal parts between raw material preparation and clinker production (25% Infrastructure investments grew by 21.5% year-on-year while real estate investments were up by 10.5%, both significantly slower than in recent years. Cement production growth fell from 9.5% in 2013 to 2.3% in 2014. China's cement industry has entered a 'new normal,' according to the country's larger producers.The cement industry of China ‘A new normal’ Global Cement
احصل على السعر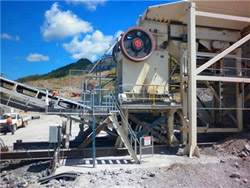
Cement IEA International Energy Agency
Cement emissions intensity has remained relatively stable since 2018, at just under 0.6 t CO 2 per tonne of cement produced, following several years of modest increase largely due to an increasing clinker-to-cement ratio in China. To get on track with the NZE Scenario, emissions must fall by an average of 3% annually through to 2030.The basic chemistry of the cement manufacturing process begins with calcination, the decomposition of calcium carbonate (CaCO 3) at about 900 °C to leave calcium oxide (CaO, lime) and liberate gaseous carbon dioxide (CO 2).This is followed by the clinkering process in which the calcium oxide reacts at high temperature (typically Recent development on the uses of alternative fuels in cement
احصل على السعر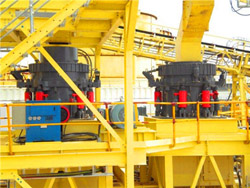
Fuels in the cement industry INFINITY FOR CEMENT EQUIPMENT
The solid fuels are: coal (anthracite), lignite, peat, wood, and coke. Coal and lignite are used in cement rotary kilns and in dryers. Coke is used in cement shaft kilns. Among liquid fuels it is heavy fuel oil which is predominantly used in cement manufacturing. Natural gas is the most common gas eous fuel in use.India is the world's second largest producer of cement and produces more than 8 per cent of global capacity. Due to the rapidly growing demand in various sectors such as defense, housing, commercial and industrial construction, government initiative such as smart cities & PMAY, cement production in India is expected to touch 550–600 million Review on vertical roller mill in cement industry & its
احصل على السعر
power plant clinker grinder crusher-coal grinder for cement
coal grinder for cement manufacturing producers . Coal Grinder For Cement Manufacturing Producers. it is also suitable for powder grinding equipment system in such industries as thermal power plant, metallurgy, chemical industry and sugar industry. Get Price. Volume 3, Issue 5, November 2013 Study of Processing andTherefore, producing cement with less energy is becoming a key element of profitability: as the grinding process consumes about 60 per cent of the total plant electrical energy demand and about 20 per cent of cement production variable cost. So efficient grinding unit selection impacts profitability of cement manufacturing.Efficient grinding unit selection impacts profitability Indian Cement
احصل على السعر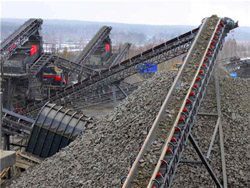
New Low-Carbon Innovations in Cement and Concrete Production
For example, PLCs use uncalcified limestone in the cement grinding phase of the manufacturing process and can reduce the carbon footprint of concrete by 5-10%. SCMs—which include things like fly ash and slag—can reduce the amount of cement required in a concrete mix, thereby reducing the carbon emissions by up to 30%.Production of Portland clinker is inherently associated with CO2 emissions originating from limestone decomposition, the irreplaceable large-scale source of calcium oxide needed. Besides carbon capture and storage, CO2 mineralization is the only lever left to reduce these process emissions. CO2 mineralization is a reversal reaction to clinker CO2 Mineralization Methods in Cement and Concrete Industry
احصل على السعر
Towards a business case for CO2 mineralisation in the cement
The cement industry, an industry characterised by low margins, is responsible for approximately 7% of anthropogenic CO2 equivalent (CO2e) emissions and holds the highest carbon intensity of anyCement manufacturing is a high energy consuming and heavy polluting process. To reduce the energy and environmental costs cement producers are currently using a blend of alternative fuels with conventional fossil fuels. process, while maximum share of electrical energy is used for cement grinding [3]. Generally fossil fuels such as Impact of Alternative Fuels on the Cement Manufacturing
احصل على السعر
coal grinder for cement manufacturing producers
Coal grinder for cement manufacturing manufacturers. Cement Manufacturing Process Phases Flow Chart . Aug 30, 2012 Kiln is heating up from the exit side by the use of natural gas and coal When material reaches the lower part of the kiln, it forms the shape of clinker Cement Manufacturing Process Phase V: Cooling and Final The German cement industry has 33 integrated cement plants, with a combined production capacity of 60.5Mt/yr. 16 It is the largest in Europe ahead of Italy (53Mt/yr), Spain (48.9Mt/yr), Ukraine (24.9Mt/yr) and France (22.6Mt/yr). The plants are owned by 13 different industrial groups, more than any other EU country.German cement focus Global Cement
احصل على السعر
(PDF) Mining Activities, Cement Production Process and
Cement has hydraulic properties like slaked lime and hardens when mixed with water. Compressive strength increases in time and reaches its practical top limit after 28 days. Mixing crushed stone
احصل على السعر