
Current Status of Copper-Ore Processing: A Review
The ore processing flowsheet includes crushing, grinding to a size of 80% passing –180 μm, the first bulk flotation with regrinding of the flotation tailings to a size of Influence of grinding on flotation of copper sulphide ores is investigated by tests in laboratory. • Milling procedure affects concentrations of Cu and Fe in the pulp A study of the effect of grinding environment on the flotation
احصل على السعر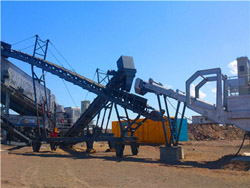
Optimizing the Rougher Flotation Process of Copper Ore
This paper focuses on optimizing the parameters of the copper ore flotation process, which is the most expensive in obtaining copper concentrate, in order to Flotation is one of the most important methods for recovering copper from copper slag, However, traditional grinding may be over grinding sometimes, resulting in Copper recovery from copper slags through flotation
احصل على السعر
Statistical investigation of flotation parameters for copper
This study is focused on the froth flotation reprocessing of a copper mineral from flotation tailings. The effects of flotation parameters including pulp density, collector The mineral composition of copper–cobalt ores is more complex than that of copper sulfides, and it is also difficult to discard tailing efficiently in primary flotation for Minerals Free Full-Text Flotation and Tailing Discarding of Copper
احصل على السعر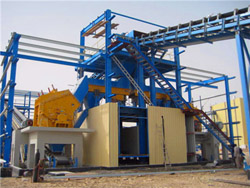
Grinding and Flotation Circuits Integration and
Following primary/secondary crushing, the material is processed through a rod/ball mill grinding circuit ahead of rougher/scavenger flotation that produces a copper concentrate.This paper presents the commercial implementation of a novel comminution circuit with high pressure grinding rolls (HPGR) followed by tower mill in a Evaluating the performance of an industrial-scale high
احصل على السعر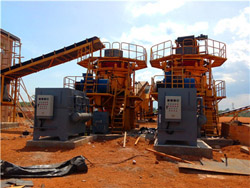
The effect of grinding conditions on the flotation of a sulphide copper
This paper describes the effect of grinding conditions on the flotation performance. Different media and mill construction materials were tested at bench scale The fresh copper oxide mineral surfaces exposed during crushing and grinding have a significant effect on subsequent flotation [23], [24], [25], [26].Many dangling bonds exist on fresh mineral surfaces because of destruction of the original lattice bonds, and the copper oxide mineral surface often shows strong polarity because of the Flotation of copper oxide minerals: A review ScienceDirect
احصل على السعر
Beneficiation an overview ScienceDirect Topics
Copper-Gold-Lead-Silver-Zinc Beneficiation Process. Beneficiation includes crushing, grinding, gravity concentration and flotation concentration. Beneficiation is followed by processing activities such as smelting and refining. The beneficiation process begins with milling, which is followed by flotation for further beneficiation.A study conducted by Gerold et al. (2012) showed that VRM was able to grind copper and slag with the energy saving of 22.9% and 34.4% respectively compared to conventional grinding circuits. Wear rate is another criterion that is needed to be considered. In this context, Erkan et al. (2012) in their study compared the wear rates of rod-ballCopper ore grinding in a mobile vertical roller mill pilot plant
احصل على السعر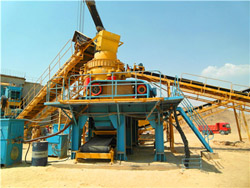
(PDF) Energy Efficiency & Copper Hydrometallurgy
The results demonstrate that hydrometallurgical processes consume significantly less energy than the alternative grinding, flotation, smelting and refining routes in many applications. HoweverThe impurities are removed, and the copper is further refined to create pure copper. Overall, the process of crushing copper ore involves mining, crushing, grinding, froth flotation, and smeltingWhat is the process of crushing copper ore? LinkedIn
احصل على السعر
Copper Ore Beneficiation Processing Technology JXSC
The processing technology of copper ore beneficiation plants includes flotation, microbial leaching, segregation, beneficiation, etc. Single sulfide ore is mostly processed by flotation, and copper ore processing equipment adopts the crushing-grinding-classification-flotation-concentration process to select single copper sulfide ore as copperThe reduction of the ore by dry crushing followed by wet grinding is essential to successful flotation. The size is correct if it is fine enough to release the bulk of the mineral from the gangue without the production of an undue amount of slime. The Inspiration Copper Co. uses flotation as the prime process, and its 800 tons per sectionFlotation 911 Metallurgist
احصل على السعر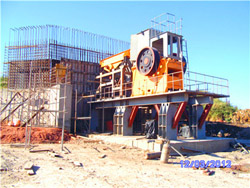
Chemical Composition Data of the Main Stages of Copper
The mining industry has faced significant challenges to maintaining copper production technically, economically, and environmentally viable. Some of the major limitations that must be overcome in the coming years are the copper ore grade decline due to its intense exploitation, the increasing requirements for environmental protection, and Flotation of Copper from Water-Quenched Converter Slags. It entails slow cooling the converter slag followed by crushing, grinding, classification, and flotation. In the second treatment beginning with a water quench (fig. 4), the crushing operation is eliminated. Evaluations are based on the processing of 500 and 1,000 tons of slag per day,How to Recover Copper from Slag by Flotation 911
احصل على السعر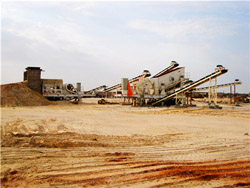
(PDF) Ferric leaching of copper slag flotation tailings
If grinding is not fine enough for efficient flotation, copper is lost in tailings. In this paper, the ferric leaching of slag flotation tailings is studied. Copper extractions of 66% are achievedCopper slag flotation process. 05-18-21; 529 Views; icon 0; The slag produced by copper pyrometallurgy in China is more than 10 million tons every year. The slag contains natural copper, a small amount of copper oxide and copper sulfide. Small flotation plants also have a conventional crushing and grinding process with three stages Copper slag flotation process Prominer (Shanghai) Mining
احصل على السعر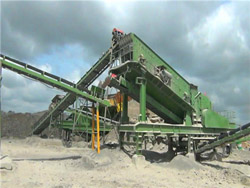
Extraction Process of Copper Sulfide Ore: A Comprehensive
The extraction process of copper sulfide ore is a complex and multi-stage process that involves various stages such as crushing, grinding, flotation, and smelting. In this article, we will provide a comprehensive guide to 3. 3. Processing of Copper Ore. Top: Sulfide ore processing. Bottom: Oxide ore processing. The process varies slightly depending on the type of ore that is being mined. Sulfide ores are first 3. Processing of Copper Ore
احصل على السعر
Copper Flotation Process And Equipment Xinhai
The copper ore flotation process includes the following stages: 1. Crushing and grinding: the copper ore is sent to the crusher and grinding equipment to be processed into small particles. This step increases the specific surface area of the ore and helps expose the copper mineral to subsequent flotation. 2.The flotation results show that the copper grade of the concentrate first increased and then decreased with the increase of the grinding time, while the recovery gradually decreased from 78.7% to 21.7%. The crushing and grinding serve either mainstream or auxiliary role in the processing of the solid wastes. This review Recovery of high-grade copper from waste printed circuit
احصل على السعر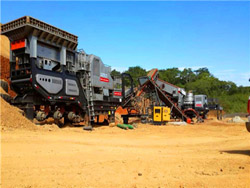
Grind Optimization of Konkola Blended Copper Ore
The grade of the concentrate is 36 to 40% TCu. The plant efficiency (recovery) is at 89% TCu. The concentrator operations include: Primary, secondary and tertiary crushing, grinding, flotation, dewatering and tailings disposal. The objective of this study was to investigate optimum grind of a blended copper ore comprising sulphide and Copper is most commonly present in the earth's crust as coppereironesulfide and copper sulfide minerals, such as chalcopyrite (CuFeS 2 Slag flotation has the advantages of more efficient Cu recovery and the possibility of using existing crushing/grinding/ flotation equipment. Select Chapter 12 Capture and Fixation of Sulfur. Book chapterExtractive Metallurgy of Copper ScienceDirect
احصل على السعر
Copper Ore Processing Plants, Flow And Equipment
2. Grinding process. The copper ore processed into granules is screened by a vibrating sieve and sent to a ball mill for grinding and crushing. Here also need to use an auxiliary equipment classifier. It can classify and screen copper ore and release copper ore powder that meets the requirements. 3.Flotation is a common mineral processing method used to upgrade copper sulfide ores; in this method, copper sulfide mineral particles are concentrated in froth, and associated gangue minerals are separated as tailings. However, a significant amount of copper is lost into tailings during the processing; therefore, tailings can be considered The Challenges and Prospects of Recovering Fine Copper
احصل على السعر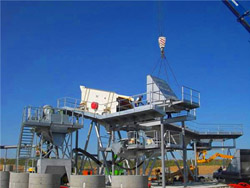
Separations Free Full-Text Improved Flotation of Fine Flake
Natural graphite ores are usually upgraded by froth flotation. However, complex processes with multistage grinding and flotation are required to achieve decent liberation and separation of graphite and gangue minerals. This study reports a short and improved flotation process for fine flake graphite ore by employing a thickening stage.
احصل على السعر