
Technical noteShould the slurry density in a grinding mill be
In the present work, the effects of some key grinding parameters such as ball size (20–40 mm), grinding time (10–30 min), solids content (65–80%), and also ore work index (12–15.4 kWh/t) on the grinding of some copper sulphide ore were investigated. The scaling and/or set-up of new grinding processes in stirred media mills often involve grinding experiments to determine the optimum grinding conditions in terms Mill, material, and process parameters ScienceDirect
احصل على السعر
Solids Choose the Right Grinding Mill Chemical
Don't choke the mill by starting with solids content that's higher than the mill can process. A rule of thumb is to start with 50% solids and adjust as needed. Remember that as particle size is reduced surface area and The flow rate selected at range of 11.5–17 t/h, slurry solid content at range of 27–61% and feed size distribution at range of 12–30 (PDF) Effects of Flow Rate, Slurry Solid Content
احصل على السعر
Measurement of Slurry Properties and Load Behaviour in Grinding Mills
This is avoided by methods 1 and 2 above. 5. Direct measurement of uM~ The viscosity, not the percent solids, of the-slurry in the mill is the parameter which The increase of slurry density from 50% to 70% solids improves size reduction as well as the use of balls of smaller size. The effect of slurry density is fairly Should the slurry density in a grinding mill be adjusted as a
احصل على السعر
An improved method for grinding mill filling ScienceDirect
The new method offers engineers and researchers a safer and faster method for quantifying the filling level in industrial SAG and ball mills, and allows the This review describes stirred media mill technologies and operating principles, and summarises stress intensity theory which can be used for selecting Stirred media mills in the mining industry: Material
احصل على السعر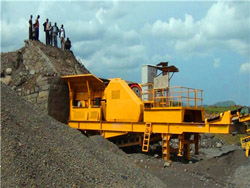
Consumption of steel grinding media in mills A review
Reliable prediction of grinding media consumption can therefore play an important role in the management and control of these costs, and the overall cost of This review describes stirred media mill technologies and operating principles, and summarises stress intensity theory which can be used for selecting Stirred media mills in the mining industry: Material
احصل على السعر
Surface area production during grinding ScienceDirect
The grinding equipment is a laboratory rod mill with internal dimensions D × L 203 × 280 mm, rotating at 72 rpm, loaded with 9 kg of rods between 12 mm and 20 mm in diameter. There were three grinding tests each one using 0.5 kg, 1.0 kg and 1.5 kg of crushed quartz respectively. In these tests the feed ratio is defined as the mass ratio of Grinding operation is widely used in solid resources processing industries such as mining, chemical, metallurgy and building materials [1][2][3] [4]. In terms of beneficiation production, grindingStirred media mills in the mining industry: Material
احصل على السعر
Energies Free Full-Text Increasing Energy
Tumbling mills have been widely implemented in many industrial sectors for the grinding of bulk materials. They have been used for decades in the production of fines and in the final stages of ore Section snippets Grinding media wear kinetics. The most widely accepted approach to characterize the slow, sustained consumption (wear) kinetics of grinding bodies in rotary tumbling mills is known as the Linear Wear Theory (Prentice, 1943; Norquist and Moeller, 1950); according to which—at every instant ‘t’ after the grinding body was Methodologies for the evaluation of grinding media
احصل على السعر
Materials Free Full-Text Optimization of the SAG Grinding
Considering the continuous increase in production costs and resource optimization, more than a strategic objective has become imperative in the copper mining industry. In the search to improve the efficiency in the use of resources, the present work develops models of a semi-autogenous grinding (SAG) mill using statistical analysis and Autogenous grinding is favored when the ore is quite competent and a fine grind is required. Semi-autogenous grinding is applied when fine crushing could cause severe problems or when ore is variable in hardness or competency. Figure 2 shows a typical conventional crushing-grinding circuit with three stages of crushing followed by Autogenous Grinding & Semi Autogenous Grinding Circuits
احصل على السعر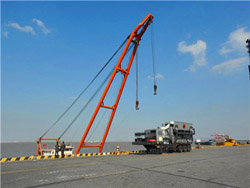
Optimization of the SAG Grinding Process Using Statistical
2. Background. The SAG grinding process has been modeled by various authors, either generating explanatory models of the grinding process, with the aim of modeling, simulating, and optimizing the individual process, as well as integrating it into aggregate processes, such as the mine-to-mill (M2M) paradigm, a practice that has An improved method for grinding mill filling measurement and the estimation of load volume and mass. The slurry is assumed to have the same solids concentration as the mill discharge (Mwansa et al., 2006). During the crash stop, the slurry level was 1.82 m below the base of the trunnion-ring, and therefore 9.08 m below the mill roofAn improved method for grinding mill filling ScienceDirect
احصل على السعر
Energy-Efficient Advanced Ultrafine Grinding of Particles
The present literature review explores the energy-efficient ultrafine grinding of particles using stirred mills. The review provides an overview of the different techniques for size reduction and the impact of energy requirements on the choice of stirred mills. It also discusses the factors, including the design, operating parameters, and feed material Grinding iron ores in conventional ball mills involve a considerably high consumption of metallic media, resulting in high operating costs. In the case of compact itabirites, the high silica content increases such consumption, potentially exceeding the costs associated with electric power consumption in industrial operations. This paper presents Study on Partial Replacement of Metal Grinding Ball with
احصل على السعر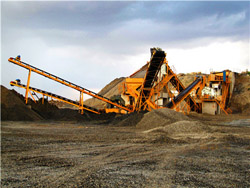
Should the slurry density in a grinding mill be adjusted as a
In the present work, the effects of some key grinding parameters such as ball size (20–40 mm), grinding time (10–30 min), solids content (65–80%), and also ore work index (12–15.4 kWh/tTransvaal, S. Africa 1988 MEASUREMENT OF SLURRY PROPERTIES AND LOAD BEHAVIOUR IN GRINDING MILLS M. H. Moys Department of Chemical EngineerinE {, L'nh1ersitJ (l the lVifLl'otersralld. P.G. ~VILTS 2050, South Afrira Abstract. The effect of slurry flowrate and viscosity on load behaviour is reviewed, and the Measurement of Slurry Properties and Load Behaviour in Grinding Mills
احصل على السعر
A Review of Alternative Procedures to the Bond
Over the years, alternative procedures to the Bond grindability test have been proposed aiming to avoid the need for the standard mill or to reduce and simplify the grinding procedure. Some of The amount of feed was set at 1175 g, which was proportional to industrial scale.The ball mill speed was constantly set at 76.8% Cs.Experiments were conducted at different ball sizes (between 20 and 40 mm), grinding time (10–30 min), solids content (65–80%) and work index of copper sulphide ore (12–15.4).RSM and Box–Behnken Investigating of the effect of ore work index and particle size
احصل على السعر
Modelling SAG milling power and specific energy
It is also possible to use the −1″ fraction that shows a positive effect on the SAG mill throughput (the power consumption decreases, but the specific energy decreases more) because the mineral goes faster to the mill discharge, leaving a greater part of the grinding task to the secondary ball mills.An hydrocyclone is to be installed in a closed circuit grinding circuit with a mill discharge containing 30% solids by volume. The solid density is 2800 kg/m 3 and the density of water is 1000 kg/m 3. Given that the maximum pressure deferential between the inlet and overflow was 50 kPa and the throughput from the mill was 800 t/h, estimate:1.Grinding Mill an overview ScienceDirect Topics
احصل على السعر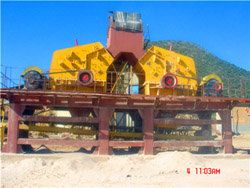
The energy efficiency of ball milling in comminution
In terms of this concept, the energy efficiency of the tumbling mill is as low as 1%, or less. For example, Lowrison (1974) reported that for a ball mill, the theoretical energy for size reduction (the free energy of the new surface produced during grinding) is 0.6% of the total energy supplied to the mill setup.71.4 % solids content i.e. 1000 g of solids and 400 g of water. Two batch grinding tests were Shortly after the first applications of closed circuit ball mill grinding it was realised that(PDF) DESIGN AND OPERATION OF VERTIMILL® FOR SECONDARY GRINDING
احصل على السعر
Fine grinding of wood Overview from wood breakage to
In wet mills (e.g. ball mills, roller mills, disc mills) grinding is performed in a particle bed in which repeating squeezing and consolidation of the bed is responsible for particle breakages [15]. Dry grinding is related to grinding where material behave more like a solid, i.e., a rigid body under compressive and shear stresses, although theThe actual milling process involves the mill that is used to break solid bulk materials into smaller pieces by grinding, cutting or crushing. Types of mills. There are a variety of mills that can be used to process bulk materials. Specific mills can grind powders and solids to any specification, as small as single-digit microns.what solids content should be used in grinding mills La
احصل على السعر