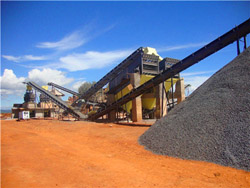
Process simulations in mineralogy-based
This study focussed on flowsheet simulation for mineralogical-based approach to geometallurgy of iron ores. Process unit models used were For this purpose, performance of two iron ore beneficiation plants with the same equipment and feed characteristics but different arrangements in the grinding and Influence of Grinding and Classification Circuit on the Performance
احصل على السعر
Existing and New Processes for Beneficiation of
Cliff’s Tilden plant in Cleveland, USA, is the only iron ore beneficiation plant, where selective flocculation technique, using degraded starch as the flocculant, has been applied to produce pellet grade The iron-making process requires high-quality raw materials, with Fe ≥ 64% and <2% alumina and silica each, to enhance blast furnace productivity at a given Iron ore beneficiation: an overview ResearchGate
احصل على السعر
Treatment of iron ore beneficiation plant process water by
Iron ore process water obtained from the beneficiation plant was treated using EC process. Impact of various operating conditions like most effective pair of the Iron will leave the system with traces of premium ore or with a poorer ore fraction in the ore beneficiation residue or as shrapnel in a dirt residue in the scrap Driving investments in ore beneficiation and scrap upgrading
احصل على السعر
A Study on High-Grade Iron ore Beneficiation to Reduce
The study here highlights the optimization of beneficiation circuit for high-grade iron ore to attain higher productivity of both Pellet Plant and Blast Furnace with the Beneficiation of Iron Ore and the treatment of magnetic iron taconites, stage grinding and wet magnetic separation is standard practice.This also applies to iron ores of the non-magnetic type which Beneficiation of Iron Ore 911 Metallurgist
احصل على السعر
Acid mine wastewater treatment using electrocoagulation
The electrocoagulation process occurs when the anode releases Al ions as an active coagulant into the solution to form floc, which binds contaminants and particles in acid mine wastewater. This could remove 99.95% of Fe in the case of wastewater from the iron ore beneficiation plant. However, until now, there are not many Al-Al electrodes usedIdiomorphic chromite is the only ore mineral appearing in economic quantities. The average content of the ore is 26% Cr 2 O 3 and the Cr/Fe ratio is 1.55. The Kemi chromium mine is an open-pit mine with a waste rock to ore ratio of 5.5:1. At Kemi, the ore from the mine contains 11% iron and 25.5% Cr 2 O 3.Chromite ore beneficiation: prospects and challenges
احصل على السعر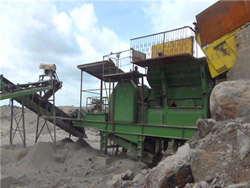
Beneficiation of Clay-Rich High-LOI Low-Grade Iron Ore
The unutilized iron ore fines (IOF, − 10 mm, 45% to < 60% Fe(T)) left at various mine sites during blasting and processing are rich in goethetic-hematite associated with high clay and considered a potential iron ore resource. The variation of loss on ignition (LOI) from mines to mines is based on the goethite and clay mineral content. The clay The earliest attempts to float iron oxide minerals involved the use of anionic collectors such as oleic acid or sodium oleate. Such a process was used at the Cuyuna Range plant which processed manganiferous iron ore in 1931. One of the successful applications of anionic flotation process was the iron ore flotation plant at Iron Ore Processing, General SpringerLink
احصل على السعر
Ore Beneficiation an overview ScienceDirect Topics
The plant separates closed-circuit crushed ROM into −31.5 Use of indigenous microorganisms isolated from an iron ore deposits makes the process cheaper, flexible, and environment-friendly. Iron ore beneficiation can be brought about through three approaches, namely, selective dissolution, microbially induced flotation, and selectiveIn India, the tailings of iron ore beneficiation are dumped in slime ponds, which is a major environmental concern. In the present study, a new beneficiation circuit was designed to recover the valuable minerals from the tailing effectively. The present study involves the characterization of three different samples using chemical, particle size, Enhanced Iron Recovery from Ultrafine Iron Ore Tailing
احصل على السعر
Existing and New Processes for Beneficiation of Indian Iron
The iron ore industries of India are expected to bring new technologies to cater to the need of the tremendous increase in demand for quality ores for steel making. With the high-grade ores depleting very fast, the focus is on the beneficiation of low-grade resources. However, most of these ores do not respond well to the conventional The plant was designed for a rated throughput of 55 million tons per year (Mta). The major part of the mined hematite iron ore is essentially contaminated with clay components and therefore requires wet processing with three comminution stages. A total of 6 parallel lines process 9500 t/h of ore.Advances in screening technology in the mining sector
احصل على السعر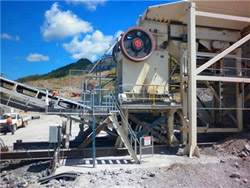
Comminution and classification technologies of iron ore
Most of the high-grade hematite iron ores are typically subjected to simple dry processes of crushing and classification to meet the size specifications required for direct shipping ore (DSO). This involves multistages of crushing and screening to obtain lump (−31.5 + 6.3 mm) and fines (approximately −6.3 mm) products.Rough processing of iron ore employs dry methods which means that equipment is tuned to process large particles, but fine magnetic material less than a few tenths of a millimeter in size is not separated as Beneficiation of Magnetically Separated Iron
احصل على السعر
(PDF) Processing of Magnetite Iron
The design outcome is a process flowsheet that specifies the required equipment and their arrangements in the beneficiation plant. The iron ore beneficiation plants normally include a seriesthe process circuits, especially gravity-based units, arises due to Figure 2—Distribution of chromite resources in India Figure 1—Chrome ore production and applications (ICDA, 2015)Process optimization of a chrome ore gravity
احصل على السعر
(PDF) Flotation of Iron Ores: A Review ResearchGate
Overview of the beneficiation process used by the Yuanjiacun iron ore concentrator, utilizing anionic reverse flotation (based on Chen, Ge and Yu 2005; Mao, Huang and Zhao 2005). FiguresPlant circuit and unit models The flowsheet used here consists of comminution and concentration circuits and is based on the LKAB Kir-una concentration plant (Söderman et al. 1996; Sams-kog et al. 1997). The circuit is a general form of the magnetite beneficiation plant that LKAB uses in Kir-una. The feed to the plant is the Process simulations in mineralogy-based geometallurgy
احصل على السعر
(PDF) Beneficiation and flowsheet development of a low grade iron ore
In the present study a detailed characterization followed by beneficiation of low grade iron ore was studied. The Run of Mine (R.O.M) sample assayed 21.91 % Fe, which is very low grade in nature.The haematite ore in South Africa is processed in a dry process to a HQ lump ore with 64 % iron content and a sintered fine ore with 63.5 % iron content. For fine ore beneficiation, wet processes are used. Capacity at the Minas Rio is to be increased from 26.5 Mta capacity to 28 Mta in the forthcoming years.Dry beneficiation of iron ore Mineral Processing
احصل على السعر
Designs of new operating copper processing plants: process
Examples of ore preparation process intensification through the use of HPGR in semi-autogenous grinding circuits are also given. The volume of impeller flotation cells installed has reached 600 m3.the Indian iron ore beneficiation process has not yet found much importance compared with those in the rest of the world. Most beneficiation plants in India are just washing material to discard liberated silica and alumina as micro fines using various stages of washing. Currently, India is at the border of a phaseDevelopment of process for beneficiation of low-grade
احصل على السعر