
Crushing characteristics and performance evaluation of iron ore
Iron ore was constructed by the second iteration method of Apollonian sphere packing. Various macro/micro properties during crushing were quantitatively characterized. Iron ore crushing and screening. Iron ore is the raw material used to make pig iron, which is one of the main raw materials to make steel. About 98% of the mined Developments in iron ore comminution and classification technologies
احصل على السعر
A Mine-to-Crusher Model to Minimize Costs at a
With the development of deep iron ore mines and underground mine explorations,harder and more compact ore is being mined now than in the past, which directly impacts operating costs. The The present work has identified an entirely new process circuit covering the crushing and grinding, and iron ore beneficiation, building on the above developments. In Transforming iron ore processing ScienceDirect
احصل على السعر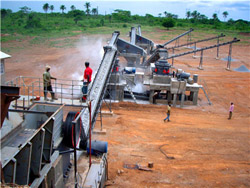
Crushing characteristics and performance evaluation of iron ore
In this study, the crushing process of spherical iron ore particles, constructed by an Apollonian sphere packing (ASP) method, was numerically reproduced in a cone crusher The combined iron ore processing technology only used for limonite, includes magnetization magnetic separation process, flotation strong magnetic separation process, gravity Extraction of Iron, Iron Mining, Iron Ore Processing Xinhai
احصل على السعر
Research into the crushing and grinding processes of
Technological cycle of iron ore crushing and grinding under production conditions is possible only in terms of mechanical load being rather labour-consuming and energy-intensive. Dry processing of iron ore: In dry processing of iron ore, ROM is generally crushed below 40 mm through three-stage crushing and thus segregated by screening Iron ore beneficiation: an overview ScienceDirect
احصل على السعر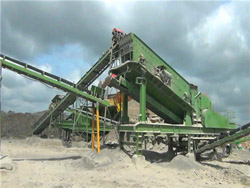
Reduction of Fragment Size from Mining to Mineral
Laboratory experiments have indicated that a larger specific charge increased both crushability and grindability of a low-grade quartz banded iron ore Dry processing of iron ore: In dry processing of iron ore, ROM is generally crushed below 40 mm through three-stage crushing and thus segregated by screening into 10–40 and −10 mm fractions. For softer ore, tumbler index is generally low and hence lump ore is crushed below 10 mm to produce 100% fine product. Yield from the plants has Iron ore beneficiation: an overview ScienceDirect
احصل على السعر
Research into the crushing and grinding processes of
A method to crush quartz-containing rocks (e.g. iron ore) providing simultaneous effect of mechanical load and UHF electric field has been developed in Dnipro University of Technology [1]. Samples of regular geometry have been tested for uniaxial and triaxial compression [2]; iron ore samples of arbitrary geometry have been tested in a laboratory大量翻译例句关于"iron ore mining" 英中词典以及8百万条中文译文例句搜索。 allocation scheme on the mining right of the iron ore mine in Aoniu District (‘‘Fushun County Liaoning Province Reinforcement — Aoniu Scheme’’) in June 2012, which is a proposaliron ore mining 英中 Linguee词典
احصل على السعر
Minerals Free Full-Text Sensor-Based Ore Sorting Technology
Graphical Abstract. 1. Introduction. Sensor-based ore sorting is gaining increased attention both within and outside the mining industry, as it is leaving the state of pilot plant scale and technology road-mapping, and an increasing amount of equipment is installed in high-capacity production scale environments.Mining of iron ore is a highly capital- and energy-intensive process. Life cycle assessment (LCA) of the mining and mineral processing of iron ore in Australia was carried out in this chapter using SimaPro LCA software as a case study. The environmental impacts considered in the study were embodied energy and greenhouse gas (GHG) Life cycle assessment of iron ore mining and processing
احصل على السعر
Why is there a need to crush iron ore bearing rock? LinkedIn
The reasons for crushing the ore-bearing rock include: Size Reduction: Iron ore typically exists in large, hard and unwieldy chunks. Crushing the ore helps reduce it to a size that can be moreThis study focussed on flowsheet simulation for mineralogical-based approach to geometallurgy of iron ores. Process unit models used were selected based on their applicability at particle level for iron ore beneficiation and flowsheet simulation. The feed streams for plant simulation were run-of-mine feed and forecast feed from ore texturalProcess simulations in mineralogy-based geometallurgy of iron
احصل على السعر
Iron processing Ores, Smelting, Refining Britannica
Iron ore sintering consists of heating a layer of fines until partial melting occurs and individual ore particles fuse together. For this purpose, a traveling-grate machine is used, and the burning of fine coke (known as coke breeze) within the ore generates the necessary heat. Before being delivered to the sinter machine, the ore mixture isThe first ore concentrate was produced at the crushing and processing complex. 1967 Construction of the mining and processing complex began. 1961 The crushing and sorting plant for sintering ore production was put into operation. 1960 The first high-grade iron ore was mined. 1957Mikhailovsky GOK Metalloinvest
احصل على السعر
The Complete Technology Book on Minerals & Mineral
such as iron ores, manganese etc. It has the world largest reserves in mica and bauxite. In the field of extractive metallurgy, mineral processing, also known as mineral dressing or ore dressing, is the process of separating commercially valuable minerals from their ores. Mining is the extraction of valuable minerals orIron ore is the key raw material for steel production enterprises. Generally, iron ore with a grade of less than 50% needs to be processed before smelting and utilization. After crushing, grinding, magnetic separation, Iron Ore Processing,Crushing,Grinding Plant
احصل على السعر
From Australian iron ore to green steel: the opportunity
The iron ore–steel value chain is energy intensive and its electrification through H₂-based DRI-EAF route will require considerable additional renewable energy generation.The feed samples of X, Y, and Z iron ores were ground in the BBM (ball mill refers to a BBM of size 300 mm × 300 mm with smooth liners) to identify the PSD, BWI, and RT of each ore. Grinding experiments were conducted according to Bond’s standard test procedure [].For each iron ore sample, the RT taken to produce 250% circulating Investigation on Iron Ore Grinding based on Particle Size Distribution
احصل على السعر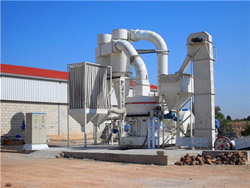
Iron ore: Mineralogy, processing and environmental sustainability
Expert analysis of quality requirements for iron production, iron ore agglomeration technologies, environmental issues, and low-emission technologies. either to prepare wet ore for crushingDOI: 10.31897/PMI.2022.61 Increasing the efficiency of crushing circuits is associated with a decrease in the particle size of finely crushed ore and the use of dry magnetic separation of crushed ore. Reducing grinding costs is achieved by using drum mills jointly with mills of other designs. The use of automation systems, slurry Iron ore beneficiation technologies in Russia and ways to
احصل على السعر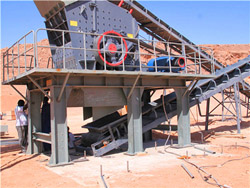
The Effect of HPGR and Conventional Crushing on the Extent
The number of micro-cracks identified in the high-pressure product (HPGR PSD 3) was 1.6 times more than the number of identified micro-cracks in HPGR PSD 1. The results show that the UG2 ore’s response to HPGR crushing conforms to the response that has been observed in other ores, e.g., zinc ore, iron ore, copper ore, and gold ore Here are the common iron ore processing technologies. marketing@ytxinhai. 0086 13810327080. Weak magnetic separation: two-and-half-block close circuit crushing and screening + one stage pre-magnetic separation for tail tossing + one stage close circuit grinding + two-block weak magnetic separation.Extraction of Iron, Iron Mining, Iron Ore Processing Xinhai
احصل على السعر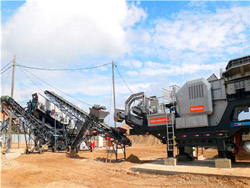
Metals Free Full-Text Effect of Iron Ore Pellet Size on
Iron ore pellets are small and hard spherical particles agglomerated from a fine iron ore concentrate. They are used in the blast furnace process to produce hot metal. The diameter of blast furnace pellets is usually between 8 and 16 mm. In this study, a batch of magnesia iron ore pellets was first sieved into particle sizes of 8–10 mm, 10–12.7 mm, The iron ore business was nearly a complete economic failure for Edison, and he lost a great deal of money. The only long-lasting impact and financial silver lining of the experiment was that Edison was able to sell the ore-crushing technology he had developed to the owners of other mines. He also used it to make cement. Partly as anEdison and Ore Refining Engineering and Technology
احصل على السعر
Comparison of fixed and mobile in-pit crushing and
In-pit crushing and conveying (IPCC) systems (whether fixed, mobile, or semi-mobile) are an alternative to the traditional truck/shovel approach to materials handling, offering potential cost savings. The greenhouse gas impact of IPCC and ore-sorting technologies. Minerals Engineering (2013) Case study on an iron ore prefeasibility
احصل على السعر