
Analysis of material flow and consumption in cement
The materials in the cyclone dust collector are divided into two parts. The primary part materials (133.93 t/h) flow into the cement mill for grinding, and then elevated to the vortex classifier. The materials from the cement mill and the cyclone dust collector Pengfei offers solutions and equipment for cement grinding plant project whose annual production capacity is 2 million tons. The cement grinding plant features leading techniques to achieve clean, Cement Grinding Plant (Annual Output: 2M tons)
احصل على السعر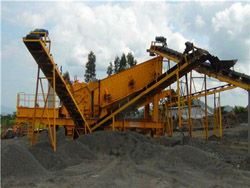
A decision support tool for cement industry to select
Plant Information. Production capacity of clinker (ton/day), Production capacity of cement (ton/day), Age (year), Altitude (meter), Electrical Specific Energy Our reference plant is a five-stage preheater-calciner kiln with a vertical raw mill and two cement ball mills. It has an annual production capacity of one million Digitization and the future of the cement plant McKinsey
احصل على السعر
Thermodynamic and exergoeconomic analysis of a cement plant
In Part 1, thermodynamic and exergoeconomic formulations and procedure for such a comprehensive analysis are provided while this paper provides an application After installation of pre-grinders, measurements revealed that specific energy consumption in raw material grinding and cement grinding decreased about 14% Energy consumption assessment in a cement production plant
احصل على السعر
Modernizing cement manufacturing in China leads to
Driven by China’s economic growth and urbanization, cement production increased significantly from 2001 to 2013 and peaked at 2476 million tons (Mt) in 2014 The increasing demand for “finer cement” products, and the need for reduction in energy consumption and green house gas emissions, reinforces the need for Cement grinding optimisation ScienceDirect
احصل على السعر
Technological Energy Efficiency Improvements in
To pursue greater energy efficiency in the cement manufacturing plants, for each operation forming the production process, a wide variety of technological solutions has been developed. For instance, The cement grinding plant is a vital link of the finished cement production. The cement grinding plant also called cement grinding unit, is used to grind clinker into qualified cement. With the development of the cement industry, cement grinding plant becomes more common. As an individual section of finished cement production, at this Cement Grinding Plant Overview Cement Grinding Unit AGICO Cement
احصل على السعر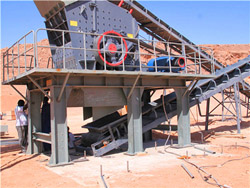
(PDF) Analysis of material flow and consumption
The results show that approximately 2.48t, 4.69t, and 3.41t of materials are required to produce a ton of the product in raw material preparation, clinker production, and cement grinding stagesThe cement industry is one of the most energy and emission-intensive sectors, accounting for approximately 7% of total-industrial energy use and 7% of global CO 2 emissions. This study investigates the potential energy savings and CO 2 abatement in the cement plants of Ethiopia. A Benchmarking and Energy Saving Tool for Cement is used Investigating energy saving and climate mitigation potentials in cement
احصل على السعر
Modernizing cement manufacturing in China leads to
Driven by China’s economic growth and urbanization, cement production increased significantly from 2001 to 2013 and peaked at 2476 million tons (Mt) in 2014 (Fig. 1b). Afterward, however, cementBall charge capacity (tons) 115. that VRM installation in grinding saves 30% of cement mill energy with ease of control and reduces approximately 3 to 6 million Btu (3.2 to 6.3 GJ) of(PDF) Determination of correlation between specific
احصل على السعر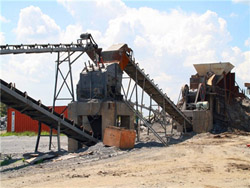
Energy Efficiency Improvement and Cost Saving Opportunities for Cement
In a dry kiln cement plant, 1993). Various new grinding mill concepts are under . development or have short tons (56.0 Mt) for dry cement and 1.2 million short tons (1.1 Mt) for otherIntroduction. Portland cement clinker is a black nodular hydraulic material. It is made by burning in a rotary kiln (pyro-processing), at least to sintering a precisely specified mixture of raw materials containing CaO, SiO 2, Al 2 O 3 and Fe 2 O 3 at temperatures of about 1400 °C. Following the clinkering process in the kiln, clinker is Optimization of an industrial scale open circuit three
احصل على السعر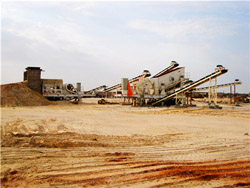
Clinker grinding technology in cement manufacturing
Clinker grinding technology is the most energy-intensive process in cement manufacturing. Traditionally, it was treated as "low on technology" and "high on energy" as grinding circuits use more than 60 per cent of total energy consumed and account for most of the manufacturing cost. Since the increasing energy cost started burning the benefitsAbout 2% of the electricity produced in the whole world is used during the grinding process of raw materials [1]. While total electrical energy consumption for cement production is about 100 kWh/ton of cement, roughly two thirds are used for particle size reduction [2]. About 65% of the total electrical energy used in a cement plant is utilizedReducing energy consumption of a raw mill in cement industry
احصل على السعر
A decision support tool for cement industry to select
Beside technological improvements, the composition of raw materials and the final product may also influence energy consumption. As shown in Fig. 1 after the crushing process, pre-blending and grinding, the raw materials are calcined to produce the semi-final product called clinker. The calcination process uses approximately 24% of the December 31, 2013 Page 1 U.S. Executive Summary The U.S. cement industry is comprised of 106 cement plants (99 clinker-producing plants and 7 grinding facilities) operating just under 100 mmt of clinker capacity and roughly 126 mmt of finishU.S. Portland Cement Industry: Plant Information Summary
احصل على السعر
11.6 Portland Cement Manufacturing U.S.
Q. Raw mill air seperator -26 R. Finish grinding mill feed belt -27 S. Finish grinding mill weight hopper -28 T. Finish grinding mill air seperator -29 U. Preheater kiln 3-05-006-22 V. Preheater/Precalciner kiln 3-05-006-23 The second step in portland cement manufacture is preparing the raw mix, or kiln feed, for theFTM Cement clinker grinding plant features. 1. Dust-free operation protects the environment. The ball mill is configured to ensure a dust-free manufacturing system and will serve to enhance your environmental conservation commitments. 2. A complete set of equipment ensures efficient and safe operation.Why and How to Build a Cement Grinding Plant in West Africa?
احصل على السعر
Reducing energy consumption of a raw mill in cement industry
While total electrical energy consumption for cement production is about 100 kWh/ton of cement, roughly two thirds are used for particle size reduction [2]. About 65% of the total electrical energy used in a cement plant is utilized for the grinding of coal, raw materials and clinker Fig. 1. The cement industry one of the worst pollutantOverall, the U.S. cement industry’s growth continued to be constrained by closed or idle plants, underutilized capacity at others, production disruptions from plant upgrades, and relatively inexpensive imports. In 2020, shipments of cement were essentially unchanged from those of 2019 and were valued at $12.7 billion. In 2020, it was estimatedCement USGS Publications Warehouse
احصل على السعر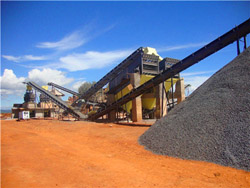
Grinding mill definition of Grinding mill by The Free
Grinding mill synonyms, Grinding mill pronunciation, Grinding mill translation, English dictionary definition of Grinding mill. A mill for grinding grain. A lapidary's lathe.Another Rs1,260 million would be invested in setting up a cement grinding mill that would have the capacity to produce up to 300 tons per hour, which would help the company convert more of its clinker into cement. And Rs1,200 million will be invested in setting up a grey cement production line with the capacity to produce 6,700 tons of As construction boom takes off, cement production reaches industry’s
احصل على السعر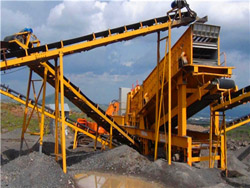
Indian Cement Sector A Hallmark of Energy Efficient
Introduction. The Indian Cement Industry has been a front runner in adopting state of the art technology, innovative process improvements and resilient business practices. It has been building sustainable societies for the future. Cement manufacturing is an energy intensive process any step/ (s) that leads to improving energy efficiencyThe cement factory where the measurements were made was located in Romania’s center-north and had a final section with two cement mills. Cement grinding was performed inside the cement mill workshop. This manufacturing phase’s product was cement—a powdery, finely ground material in closed-loop tubular ball mills (Figure 1). Dust Emission Monitoring in Cement Plant Mills: A Case
احصل على السعر
DG Khan Cement announces completion of Pakistan’s biggest $300mln plant
KARACHI: DG Khan Cement on Wednesday announced the start of the country’s biggest cement plant with around 9,000 tons/day capacity at an estimated cost of over $300 million as construction...
احصل على السعر